机床立柱是机床重要的结构件,起着支撑横梁上下运动的作用。根据立柱的结构特点和技术要求,以及企业生产实际,确定了合理的工艺方案,包括铸件分型面、浇注位置,各类工艺参数和浇注方法等,生产出合格的大型立车立柱,满足了立柱的技术要求。
大型数控立式车床(以下简称“立车”)立柱是机床的关键基础零部件,立柱主要对立车横梁、刀架体及滑枕等参与切削加工的部件起支撑和稳定的作用,满足横梁沿立柱导轨的Z向运动,并在间接承受切削力、振动、温度变化等恶劣条件下工作。为满足数控立式车床的加工要求,立车立柱要求具有足够高的构件强度和刚度,良好的抗振性和抗热变形能力,所以其结构刚性、减振性能、导轨面硬度等方面要求较高,使得立车立柱的工艺设计和生产制造难度较大。
1.1 立车立柱的主要结构特点
立车立柱内部是多层结构、强度高,轮廓尺寸大、加工行程长,壁厚不均匀、生产难度大,属于超大、超重型、高强度灰铸铁件。铸造过程中体积大、结构复杂,浇注的铁液量多,铸件冷却时间长,易出现缩孔、缩松、气孔、裂纹、力学性能不达标等铸造缺陷,并且生产过程控制难度较大。因此,对工艺设计提出了更高的要求。笔者以轮廓尺寸为11 000 mm×2 600 mm×1 250 mm,净重42 750 kg,毛重46 500 kg,最小壁厚35 mm,最大壁厚154 mm的立车立柱为例展开研究,其结构如图1所示。
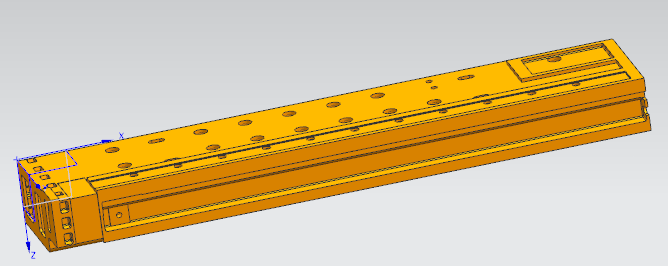
图1 立车立柱
1.2 立车立柱的技术要求
铸件的材质为HT250,立柱导轨硬度180~230 HBW,立柱导轨面不允许有缩孔、裂纹、砂眼、夹砂等铸造缺陷。
根据立车立柱铸件结构特点及主要导轨面的技术要求,从造型材料及造型方式、铸件的工艺性、分型位置选取、砂芯设计、浇注系统设计等方面进行工艺分析和设计。
2.1 造型材料及造型方式
采用树脂砂生产铸件具有尺寸精度高、表面光洁度好的优势,但同时也存在易粘砂、易出现气孔等问题,特别是大型铸件铁液量大,凝固时间长,更易产生这些缺陷。因此,在生产中需要控制好再生砂的质量,同时增加砂型的排气,减少砂型的发气量。
根据立柱的结构特点、尺寸大小及实际生产条件,采用地坑实样造型。
2.2 铸件的工艺性分析
对立柱的铸造工艺性进行分析后发现,立柱背面直角处结构容易开裂,建议设计人员采用斜面过渡,同时在壁厚的急剧变化处,增加了工艺拉筋,以防止裂纹的出现。
运用铸造数值模拟,分析导致铸件厚大部位、导轨面等产生缩孔、缩松等缺陷趋势的原因,优化浇注系统、冒口、冷铁设计,保证铸件各部冷却均衡,以减小铸造应力,防止铸件产生裂纹和缩孔、缩松缺陷。
2.3 铸件分型面的选取
分型面的确定应考虑:质量要求较高的表面应放在下面或侧面;铸件的大平面应放在下面;有利于铸件实现方向性凝固及便于放置补缩冒口;为减少披缝和错箱,保证铸件尺寸及外观质量,铸件应尽量置于同一砂型中。
根据分型面的选择原则及立柱的结构特点、技术要求、生产条件等,为保证立柱导轨面质量,以及实现补缩,立柱的分型面和浇注位置见图2。
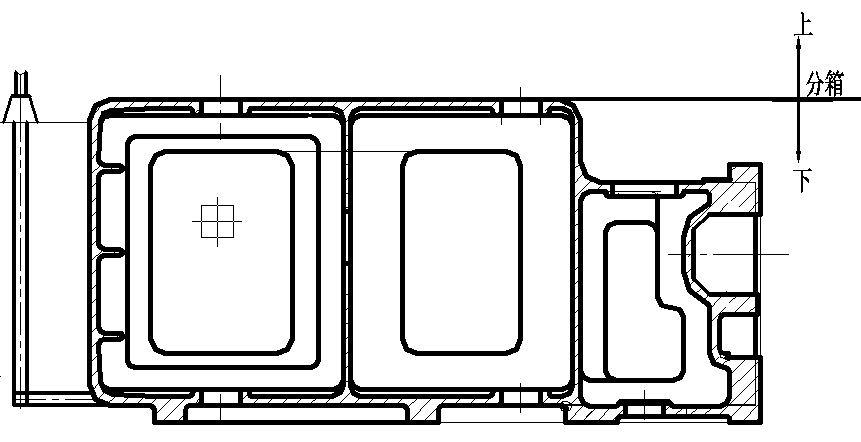
图2 立柱浇注位置
2.4 铸件的砂芯设计
砂芯设计应尽量减少砂芯的分割和芯撑的使用;要便于从制芯到下芯的过程和砂芯出气;另外,砂芯定位要准确、固定要牢靠。立柱内腔结构复杂、尺寸大,砂芯数量达37个,由于两端砂芯上部没有出气孔,因此通过连接侧面的出气道来排气。
2.5 铸件的浇注系统设计
立柱浇注系统采用底注式,铁液从立柱的下平面进入型腔,如图2所示。采用底注式浇注系统,金属液充型较平稳,液面是逐渐升高的,避免了冲击、飞溅和氧化,有利于铁液中杂质的上浮及型腔内气体排出,从而有效防止了铸件导轨产生渣、气孔等缺陷。
用浇注比速来计算浇注系统的尺寸。此法可用于各种合金、各类铸件的浇注系统计算,主要用在大型和重型铸件上。
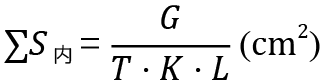
式中,G为流经S阻流截面的液体金属质量(kg);T为浇注时间(s);K为单位面积的浇注速度(kg/cm2·s);L为金属液流动系数。笔者选取铸件液体金属质量为52 000 kg,浇注时间为206 s,浇注速度为0.9 kg/cm2·s,金属液流动系数取1。
通过公式计算,同时结合铸件结构特点及实际生产经验,浇注时要快速充满铸型,取∑S内=281 cm2。
(b)浇注系统采用半封闭式浇注系统。半封闭式浇注系统充型快,挡渣效果好,不易卷入气体。根据实际生产经验公式,∑S直=1.2×∑S内=337 cm2;∑S横=1.4×∑S内 =393 cm2。
2.6 冒口、冷铁设置
立柱导轨和上下端面螺包处壁厚大,易形成缩孔、缩松,需要采用冒口进行补缩,为保证两导轨补缩顺畅,两导轨之间还采用过道进行连接。为防止缩孔、缩松,立柱共设置了方形明冒口20个。
为防止缩孔、缩松,保证立柱导轨组织致密和冒口的补缩距离,在导轨等厚大部位设置外冷铁进行激冷,整个立柱共放置了256块外冷铁。
2.7 其他工艺参数的选择
根据铸件尺寸大小、结构特点,铸件的机械加工余量按GB/T 6414-2017选取。
根据铸件的结构特点及环境条件,选取开箱时间为浇筑后368 h,选取立柱的保温时间为392 h。
针对优化后的工艺设计,编制铸件生产过程控制方案和现场施工方案,跟踪生产过程,确保浇冒系统等与工艺要求一致,做好工艺验证工作。
3.1 造型、合箱控制
(1)造型控制
根据要求使用合格的型、芯砂,保证型、芯砂24 h抗拉强度不低于0.8 MPa。造型、制芯过程填砂时,采用分层填砂。每层厚度控制在200 mm左右,用木棒等充分紧实,砂型不易到达的部位用手捣实。砂芯修整完清理干净后放置4 h以上,采用流涂方式涂刷醇基涂料,砂型在起模4 h后涂刷醇基涂料,保证涂料的厚度约为1 mm,易粘砂部位应适当加厚。
合箱前要验箱,确保分型面及出气芯头坭条充分压实,保证盖箱等出气孔通畅,合箱后正确放置浇口杯,使浇口杯与盖箱直浇道对齐,并防止杂物进入浇冒口系统及型腔。
3.2 熔化、浇注方案
根据铸件的材质及结构确定化学成分,见表1,保证铸件性能达到设计要求。
表1 立柱熔炼时化学成分(质量分数,%)

(2)浇注方案
浇注时采用两包浇注,两包铁液温度要尽量一致,温差不超过20 ℃。出炉温度>1 450 ℃,浇注温度控制在1 320~1 340 ℃。
采用上述造型、扣箱、浇注等方案生产出来的立车立柱,加工后情况如图3所示,铸件没有出现缩孔、缩松、裂纹等铸造缺陷,试棒检测、本体检测金相组织和力学性能均符合GB/T 9439-2010、GB/T 7216-2009要求。目前已按此方案进行批量生产。
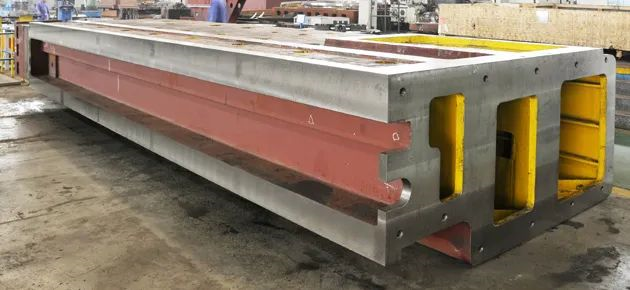
图3 立柱加工后情况
大型数控立式车床的立柱由于尺寸长,内部结构复杂、筋板多且分层,铁液充型的行程较长、铸件冷却时间长,易产生冷隔、缩孔、缩松、气孔、裂纹、力学性能不达标等铸造缺陷。对于这种大型铸件的生产,要结合实际生产条件、生产能力、零件的技术要求、结构特点等各方面的因素进行工艺分析和优化,确定合理的铸造工艺方案、同时严格控制生产过程,才能确保铸件的质量达到设计要求。