编辑导语:介绍了高速冲床球墨铸铁圆盘铸件的化学成分、造型工艺、浇注系统与冷铁、球化与孕育处理、熔炼浇注等工艺方案。采用AnyCasting软件对充型和凝固过程的进行了模拟分析。通过生产验证获得了金相组织和力学性能满足要求的铸件。分析认为,对于冲床类铸件化学成分应控制碳当量4.0%~4.2%、硅2.1%~2.3%、锰≤0.5%,残余镁含量0.035%~0.055%,稀土0.01%~0.02%;采用多次孕育,选取钇基重稀土球化剂,缩短凝固时间;采用底注多内浇道分散设置,保证铁液充型平稳,冷铁加强关键部位冷却,减少缩松缺陷,提高铸件的组织致密度和力学性能。
圆盘铸件是高速冲床至关重要的部件,高速冲床的主体由飞轮圆盘组成,其周面上设有若干方槽,主要起减重作用,圆盘底部设有6个工艺孔,与筋板连接处为圆弧段,为了确保冲床冲压力度始终均匀,延长其使用寿命,圆盘不能变形。
圆盘毛坯质量38 000 kg,三维结构见图1所示,铸件总高度1 700 mm,圆盘外径4 800 mm,最大尺寸5 820 mm,主要壁厚为220 mm,轴承座孔根部壁厚最大,属于热节区域。圆盘材质为QT500-7,单铸试棒要求力学性能为抗拉强度大于420 MPa,屈服强度大于320 MPa,断后伸长率大于5%。铸件下表面有一圈螺纹孔,与盖配合,要求孔内无疏松缺陷。因铸件空腔面积大,铸造工艺困难。
球墨铸铁具有较大的氧化倾向,为保证铁液充型平稳防止湍流、减少夹渣和气孔等缺陷,大型铸件一般采用底注式、半封闭式浇注系统,另外圆盘铸件模数较大,理论上通过保证树脂砂砂型强度、加强铁液随流孕育等措施,可达到无冒口铸造。根据碳当量CE决定C和Si的含量,一般来说选择C含量为3.5%左右。P是正偏析元素,又是促进碳化物形成元素,含量应尽可能低,要求P≤0.02%。不同的S含量,所需的Mg残量是不同的,只有低的S含量才能保证在较低的Mg残含量(0.035%~0.055%)下获得2级以上的球化效果,一定要保证原铁液的S<0.015%,最好控制在0.01%以下。
消耗Mg类,如Ti、S、O、Te、Se等元素。消耗Mg或在石墨球长大过程中直接干扰Mg的球化作用;正偏析碳化物形成元素,如Mn、Cr、Mo、V、P等。对于大断面球墨铸铁来说,加入微量干扰元素(如Sb、Bi等),不但对球化没有影响,还能增加石墨球数和球化率,消除碎块状石墨,一般加入量控制在0.005%~0.01%,因超过此含量,则其破坏球化的作用又表现出来。

采用呋喃树脂砂,三箱造型,分型方式如图2所示。浇冒口系统工艺设计示意图见图3。
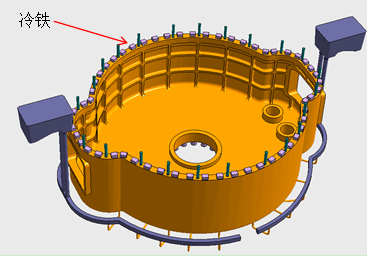
为保证圆盘底面的材料致密性,同时使得铁液充型平稳,减少冲砂风险,将底面置于下箱,金属液通过内浇道从圆盘底面注入。为减少浇注系统与砂型的碰撞,使用随型横浇道。
大模数球墨铸铁的凝固时间长,常会降低石墨球化率,或导致石墨畸变、石墨漂浮、石墨粗大等缺陷,故需采用冷铁缩短其凝固时间。圆盘热节主要集中在底部,如图3所示,由于结构限制,不适合放置冒口,于是在工艺设计时,以冷铁为主,针对厚大断面球墨铸铁件的铸造,冷铁的使用非常关键,不仅可以加强冷铁附近区域铸件的冷却,改善金相组织,防止石墨衰退,另外在充型时,不断降低相接触铁液的温度,让铁液的液态收缩提前,从而得到浇注系统的及时补缩,尽量减小铸件在浇注系统凝固后的收缩量。
采用球墨铸铁大件工艺设计原则,浇注铁液的质量约为40 000 kg,最终选取的浇注系统各单元截面比例约为A直:A横:A内=1:1.2:0.8,用以保证铁液大流量、平稳。
厚大断面球墨铸铁件,因其球化衰退导致产生石墨畸变及碎块状石墨,数据表明Mg残含量提高至0.05%~0.07%,结果并不理想,Mg残含量的增加反而使球墨铸铁的缩松与夹渣废品显著上升。因此,厚大断面球墨铸铁最后凝固的球化衰退不能用Mg的逃逸衰退来解释,其主要原因是与球墨铸铁中的S含量有关,S含量越高球化衰退越快,反之越慢,因此将S含量控制在较低水平是抗球化衰退的重要措施,在保持一定的Mg残含量的情况下,将球化后S含量控制在0.006%~0.01%。对于圆盘铸件,采用冲入法球化。球化剂选用钇基重稀土球化剂,主要元素及加入量见表2所示。
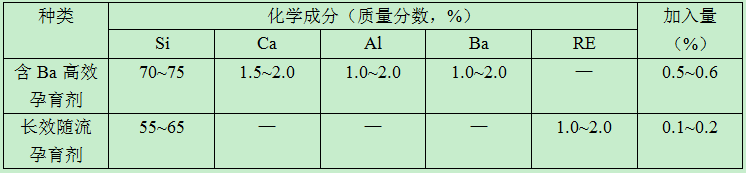
厚大断面球墨铸铁件的多次孕育与中小球墨铸铁件孕育有3点不同:一是出铁孕育时孕育量大;二是浇包是20~60 t的大包,孕育后难以搅拌;三是浇注时由于铁液量多达几十吨,随流孕育难度大。孕育是防止厚大断面球墨铸铁石墨畸变、出现碎块状石墨的有效措施。孕育时需要注意两个问题:一是原铁液中S的含量不能过低,应大于0.006%,铁液中O的含量不能过低,应大于0.001%,否则影响孕育效果;二是控制Si总的含量不可过高,因为球化剂中的Si含量一般为45%左右,孕育剂中的Si含量大于70%。采用多次孕育处理,选用含Ba高效投掷孕育剂和长效随流孕育剂,主要元素及加入量见表3所示。
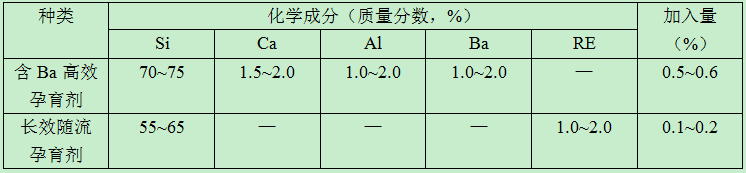
低温浇注能缩短厚大球墨铸铁件凝固时间,改善其石墨形态,在实际生产中,为了获得低的浇注温度而又不至于加长铁液保持时间引起孕育衰退,采用倒包等措施使铁液快速降温。圆盘的熔炼温度控制在1 500~1 550 ℃,过热静置5~8 min,净化铁液,出炉温度控制在1 430~1 460 ℃,为缩短凝固时间,同时减小液态收缩,可适当降低浇注温度,但过低的浇注温度不利于铁液中的夹渣和气体等上浮,甚至形成冷隔,因此综合考虑将浇注温度定为1 300~1 330 ℃。
采用AnyCasting软件对铸造工艺进行充型和凝固过程的模拟,模拟结果显示铁液进入型腔后,充型无较明显飞溅,较为平稳;充型40%时,铸件内铁液平均速度为51 cm/s,趋于平稳,无冲砂风险;充型结束时,氧化夹杂风险降低;铁液温度下降50 ℃,温差较小,无冷隔风险。
图4为充型顺序的仿真结果,从图中可以看出,金属液充填12 s时,内浇道进水口处存在孤立液相岛,有喷溅倾向,此处与内浇道末端时间相差24 s,较为安全。充型43 s时,铁液到达型腔各位置时间较为均匀,充型平稳。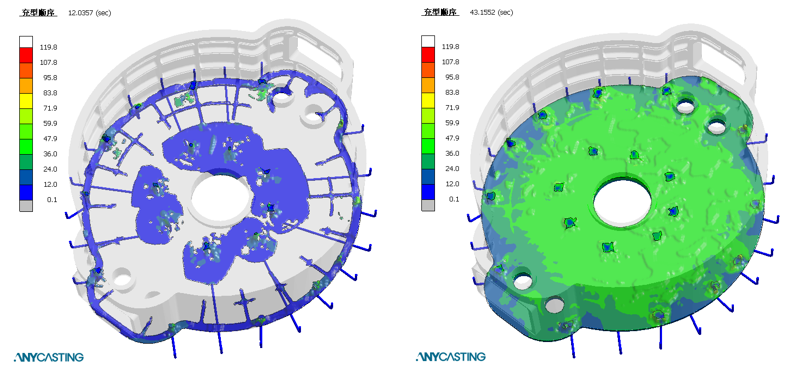
(a)金属液充填12s时的模拟结果 (b)金属液填充43s时的模拟结果
图5为充型速度场的仿真结果,从图中可以看出,充型14%时,内浇道进水口处速度160 cm/s,速度适中,充型40%时,铸件内平均速度为51 cm/s,速度趋于平稳,无冲砂风险。
(a)充型14%时的速度场 (b)充型40%时的速度场
图6为充型过程中氧化物的仿真结果,从图中可以看出,充型17%时,轴承座孔工艺台氧化物含量4.2 g/cm3,存在氧化夹杂风险,充型结束时,铸件上表面氧化物含量3.58 g/cm3,氧化夹杂风险降低。
(a)充型17%时的氧化物 (b)充型100%时的氧化物
图7为充型温度场的仿真结果,从图中可以看出,充型至26%时铁液温度下降30 ℃,充型结束时铁液温度下降50 ℃,温差较小,无冷隔风险。
(a)充型26%时的温度场 (b)充型100%时的温度场
按照上述工艺过程进行试制,获得铸件的化学成分、力学性能和组织的检测结果见表4、表5和图8。


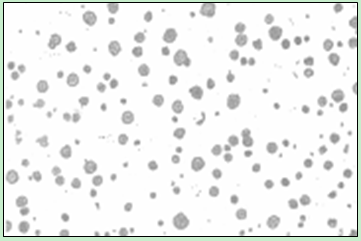
(a)腐蚀前金相
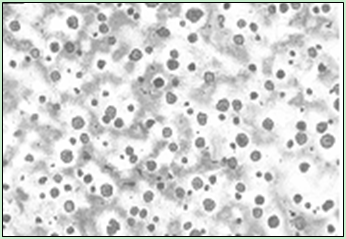
试验结果显示,附铸试块性能达到技术要求,首件经机加工验证无缺陷,铸件成品如图9所示,并通过工艺过程评定后,最终对其铸造工艺进行固化。
(1)对于冲床球墨铸铁圆盘铸件,合适的化学成分(质量分数)为碳当量4.0%~4.2%、硅2.1%~2.3%、锰≤0.5%,残余镁含量控制在0.035%~0.055%,稀土元素控制在0.01%~0.02%。(2)采用多次孕育,选取钇基重稀土球化剂,出炉温度控制在1 430~1 460 ℃,缩短凝固时间,可以改善石墨球分布及形态。(3)针对大型球墨铸铁件,尽量采用底注多内浇道分散设置,保证铁液充型平稳,冷铁加强关键部位冷却,消除或减轻缩松缺陷,提高铸件的组织致密度和力学性能。